The fathers of quality, Deming and Shewhart
In the 1980s, there was a prevailing thought in popular culture that Japan would take over the world — not by force, but by its vigorous economy, which was the second largest in the world between 1990 and 2010. We can see this in many movies, such as Back To The Future Part II, where Marty McFly has a Japanese boss in the future; and in Die Hard, where John McClane's wife works for a Japanese company. Her boss is Mr. Takagi, in the picture below.
The keyword that summarizes the Japanese economic miracle is quality. By focusing on better products, with fewer defects and more efficient processes, their industry gained the attention of consumers and space in the global economy.
This transformation began with two men, whose works changed Japan and companies around the whole world.
Deming and Shewhart
William Edwards Deming (1900-1993) was an American statistician, engineer, economist and consultant. For his work, he is known as the father of quality.
Deming graduated in electrical engineering and later specialized in mathematical physics. In 1927, he started working in the United States Department of Agriculture, and there, through colleagues, he met Walter Andrew Shewhart (1891-1967), who is known as the father of statistical quality control. Shewhart was an engineer of Bell Telephone Company and used statistics to improve the reliability and voice clarity of telephone lines.
Shewhart taught Deming many tools that served as the basis for his future works, among them, control charts and PDCA cycles.
Control chart
Shows how much something stays within a margin of tolerance over time.
Some real-life examples: the size of produced mechanical parts; the amount of active ingredient in each tablet; the travel time between two cities.
Below, we see a process that is initially out of control; later, it stays within the tolerance zone; and finally, within a tighter zone, indicating an improvement on the quality of the process.
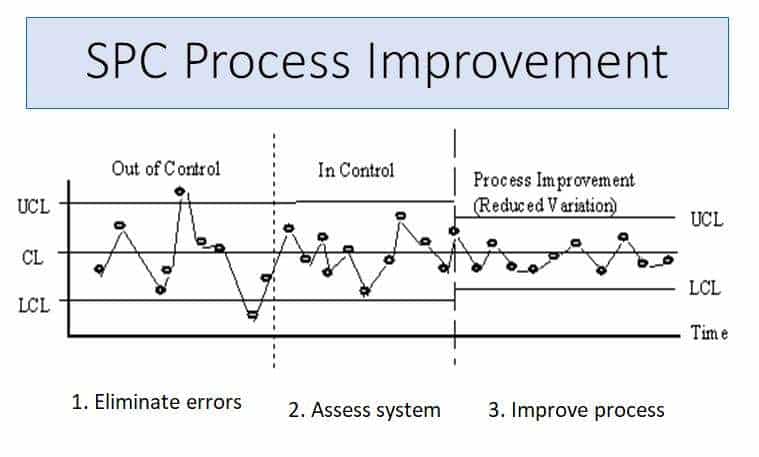
With a control chart we can detect anomalies in a production line, or estimate when a machine will need maintenance.
Second World War and post-war
During World War II, Deming was part of the U.S. Emergency Technical Committee, focused on improving the wartime production. Statistical quality control was used on factories and reduced the number of failures in American weaponry.
After the war, Deming was convoked to prepare the 1951 Japanese census and his effort and involvement in Japanese society caught attention, to the point that the Japanese Union of Scientists and Engineers (JUSE) invited him to teach them about statistics and quality. His lessons were a tremendous success and were transcribed into books with thousands of copies sold.
In a lecture to Japanese executives in 1950, Deming told them that implementing statistical quality control on their companies would lower costs and waste, increase productivity and attract consumers, allured by better products. The executives applied these ideas into their businesses and had very positive results.
In the following decades, Japan witnessed its economy rise from the ashes and become one of the largest in the world, largely due to the implementation of Deming's ideas. The GDP growth was around 8-10% yearly.

Case study: Mazda-Ford transmissions
In the 80s, Ford partnered with Mazda to produce automatic transmissions for Ford automobiles.
Both companies produced this transmission and in both of them the products had full specification conformance. Despite that, Ford transmissions had a higher number of customer complaints and incurred higher repair costs; not just that, customers came over to Ford dealerships asking for their new cars to have Japanese transmissions, because they had a smoother driving experience.
Ford engineers investigated and noted that Ford transmissions had a variance of 70% within the margin of tolerance, while Mazda transmissions had a variance of 27%. For example, if the specification of a part was 300mm ± 3mm, Ford's parts size varied by 2.1mm; while Mazda's varied by 1.15mm.
Mazda's production cost was slightly more expensive, but compensated by having less warranty claims.
After this study, the Ford factory improved the quality of its transmissions, that became better than Mazda's.
Case study: Sony TVs
Also in the 1980s, Sony had two TV production plants, one in Japan and one in San Diego, California.
One of the quality factors for a TV was the colour density, with a margin of tolerance between 9 and 14. TVs made in San Diego all were within tolerance, while 1.3 for every 1000 of the ones made in Japan were out. Regardless of that, consumers preferred Japanese TVs, because the image on the screen was more homogenous and with a better resolution, due to a lower variance of colour density.
Recognition in the U.S.
Ironically, Deming's ideas fell into disuse in the United States after the war and were not widely accepted by American executives, who believed that quality was a cost, rather than an investment.
In the following decades, Deming extended his work for beyond statistics and addressed how to improve the efficiency and organization of companies, summarizing his ideas in 14 points for management.
In 1980, NBC aired a documentary comparing American and Japanese companies. Deming was interviewed in this documentary, and after his appearance on TV, many corporations requested Deming's consultancy services. One of the companies that hired him was Ford.
At the beginning of the 1980s, Ford was facing a major crisis, with losses exceeding $3 billion. Deming was called and said that the management was responsible for 85% of the problems in developing better cars. Ford executives took this seriously and adopted Deming's ideas: by 1986, Ford became the most profitable American auto company, surpassing General Motors for the first time since the 1920s. Revenue grew consistently over the following years.
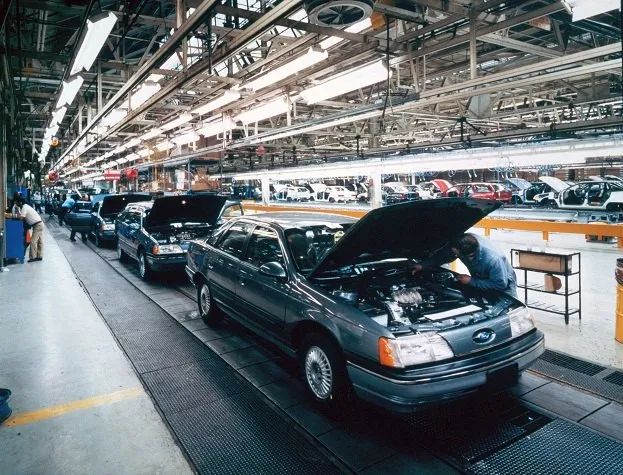
14 points for management
In his book Out of the Crisis, Deming presents the following points for transforming business effectiveness:
Create constancy of purpose toward improvement of product and service, with the aim to become competitive, to stay in business and to provide jobs.
Adopt the new philosophy. We are in a new economic age. Western management must awaken to the challenge, must learn their responsibilities, and take on leadership for change.
Cease dependence on inspection to achieve quality. Eliminate the need for massive inspection by building quality into the product in the first place.
End the practice of awarding business on the basis of a price tag. Instead, minimize total cost. Move towards a single supplier for any one item, on a long-term relationship of loyalty and trust.
Improve constantly and forever the system of production and service, to improve quality and productivity, and thus constantly decrease costs.
Institute training on the job.
Institute leadership. The aim of supervision should be to help people and machines and gadgets do a better job. Supervision of management is in need of overhaul, as well as supervision of production workers.
Drive out fear, so that everyone may work effectively for the company.
Break down barriers between departments. People in research, design, sales, and production must work as a team, to foresee problems of production and usage that may be encountered with the product or service.
Eliminate slogans, exhortations, and targets for the work force asking for zero defects and new levels of productivity. Such exhortations only create adversarial relationships, as the bulk of the causes of low quality and low productivity belong to the system and thus lie beyond the power of the work force.
a) Eliminate work standards (quotas) on the factory floor. Substitute with leadership.
b) Eliminate management by objective. Eliminate management by numbers and numerical goals. Instead substitute with leadership.Remove barriers that rob the hourly worker of his right to pride of workmanship. The responsibility of supervisors must be changed from sheer numbers to quality.
Remove barriers that rob people in management and in engineering of their right to pride of workmanship. This means, inter alia, abolishment of the annual or merit rating and of management by objectives.
Institute a vigorous program of education and self-improvement.
Put everybody in the company to work to accomplish the transformation. The transformation is everybody's job.
Sources and interesting reads
- TV Tropes - Japan Takes Over The World - Analysis
- Wikipedia - List of countries by largest historical GDP
- Die Hard characters photo
- BizManualz - How to Use Control Charts for Continuous Improvement
- Wikipedia - William Edwards Deming
- Wikipedia - Walter Andrew Shewhart
- The Deming Institute - The Man
- National Academy of Engineering - W. Edwards Deming
- YouTube - NBC documentary "If Japan Can, Why Can't We?" (1980) (recommended)
- Deming's 1950 Lecture to Japanese Management
- Spec Innovations - Ford vs. Mazda transmissions
- Elsmar Quality Forum - The Famous Ford Study of Mazda Transmissions - Can the characteristic be measured?
- New York Times - Management: Ford Embraces Six Sigma (06/13/2001)
A
AlexandreHTRBCampinas/SP,
Brasil