Os pais da qualidade, Deming e Shewhart
Nos anos 1980, havia um pensamento na cultura pop que o Japão conquistaria o mundo — não pela força, mas por sua economia pujante, que foi a segunda maior do mundo entre 1990 e 2010. Podemos ver isso em vários filmes, como no De Volta Para o Futuro Parte II, em que o chefe do Marty McFly no futuro é japonês; e em Duro de Matar, em que a esposa do protagonista trabalha numa empresa japonesa, no fim da década de 80. O chefe dela é o Sr. Takagi, na imagem abaixo.
A palavra-chave que resume o milagre econômico japonês é qualidade. Ao focar em produtos melhores, com menos defeitos e com processos industriais mais eficientes, a indústria japonesa ganhou a atenção dos consumidores e espaço na economia global.
Essa transformação começou com dois homens, cujos trabalhos mudaram o Japão e as empresas de todo o mundo.
Deming e Shewhart
William Edwards Deming (1900-1993) foi um estatístico, engenheiro, economista e consultor americano. Por seu trabalho, ele é conhecido como o pai da qualidade.
Deming fez graduação em engenharia elétrica, e depois mestrado e doutorado em matemática e física. Em 1927, ele começou a trabalhar no Departamento de Agricultura dos EUA e lá, por meio de colegas, conheceu Walter Andrew Shewhart (1891-1967), este que é conhecido como o pai do controle estatístico de qualidade. Shewhart era um engenheiro da Bell Telephone Company e usava estatística para melhorar a confiabilidade e clareza sonora das linhas telefônicas.
Shewhart ensinou a Deming muitas ferramentas que serviram de base para seus trabalhos futuros, dentre elas, os gráficos de controle e os ciclos PDCA.
Gráfico de controle
Mostra quanto algo fica dentro de uma margem de tolerância ao longo do tempo.
Alguns casos da vida real: o tamanho de peças mecânicas produzidas; a quantidade de remédio inserida em cada comprimido; o tempo de trajeto entre duas cidades.
Abaixo, vemos um processo que inicialmente está fora de controle; depois, fica dentro da zona de tolerância; e por fim, dentro de uma zona mais estreita, denotando melhora na qualidade do processo.
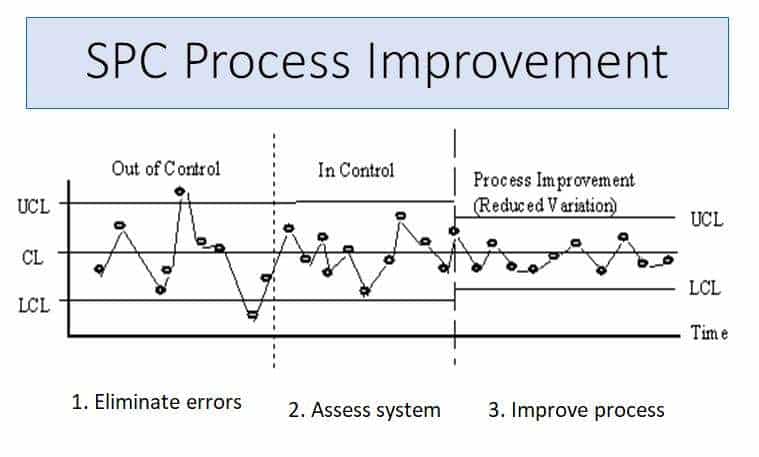
Com um gráfico de controle podemos detectar anomalias numa linha de produção, ou então estimar quando uma máquina precisará de manutenção.
Segunda Guerra Mundial e pós-guerra
Durante a Segunda Guerra Mundial, Deming fez parte do Comitê Técnico Emergencial dos EUA, focado em melhorar a indústria armamentícia. O controle estatístico de qualidade foi aplicado nas fábricas e diminuiu o número de falhas em armamentos americanos.
Após a guerra, Deming foi convocado para preparar o censo japonês de 1951 e seu trabalho e envolvimento na sociedade japonesa o fizeram ser notado, a ponto de a União Japonesa de Cientistas e Engenheiros (JUSE) chamá-lo para lhes ensinar sobre estatística e qualidade. Suas aulas foram um tremendo sucesso e foram transcritas em livros com milhares de cópias vendidas.
Em uma palestra a executivos japoneses em 1950, Deming lhes disse que implementar o controle estatístico de qualidade nas suas empresas diminuiria custos e desperdícios, aumentaria a produtividade e cativaria os consumidores, atraídos por produtos melhores. Os executivos levaram essas idéias para suas companhias e tiveram resultados muito positivos.
Nas décadas seguintes, o Japão viu sua economia ressurgir das cinzas e ganhar destaque mundial, em grande parte devido à implementação das idéias de Deming. O crescimento do PIB girava entre 8-10% ao ano.

Caso de estudo: Transmissão Mazda-Ford
Nos anos 80, a Ford fez uma parceria com a Mazda para produzir câmbios automáticos para carros da Ford.
Ambas as companhias produziam essa transmissão e nas duas os produtos saíam de fábrica dentro das margens de tolerância. Contudo, transmissões Ford recebiam mais reclamações de clientes e tinham reparos mais caros; não só isso, as pessoas chegavam às concessionárias da Ford pedindo que seus carros novos viéssem com transmissão japonesa, pois eram mais macios de dirigir.
Os engenheiros da Ford investigaram e notaram que as transmissões Ford tinham variância de 70% da margem de tolerância, enquanto que as transmissões Mazda tinham variância de 27%. Por exemplo, se a especificação de uma peça era de 300mm ± 3mm, na Ford as peças variavam 2,1mm; na Mazda, 1,15mm.
O custo de produção na Mazda era um pouco mais caro, porém, o custo de arcar com a garantia na Ford era maior.
Após esse estudo, a fábrica da Ford melhorou a qualidade das suas transmissões, que se tornaram melhores do que as da Mazda.
Caso de estudo: TVs da Sony
Também nos anos 80, a Sony tinha duas plantas de produção de TVs, uma no Japão e outra em San Diego, Califórnia.
Um dos parâmetros de qualidade era a densidade de côr, com margem de tolerância entre 9 e 14. As TVs produzidas em San Diego todas estavam dentro da margem, enquanto que 1,3 em cada 1000 das produzidas no Japão estavam fora. Todavia, os consumidores preferiam as TVs japonesas, pois a imagem na tela era mais homogênea, devido a uma menor variância de densidade de côr.
Reconhecimento nos EUA
Ironicamente, as idéias de Deming caíram em desuso nos EUA após a guerra e não tiveram aceitação entre os executivos americanos, pois eles acreditavam que qualidade era um custo, e não um investimento.
Nas décadas seguintes, Deming estendeu seu trabalho para além da estatística, abordando como melhorar a eficiência e organização nas empresas, resumindo suas idéias nos chamados 14 pontos para gestão.
Em 1980, a NBC produziu um documentário comparando empresas americanas e japonesas. Um dos entrevistados foi Deming, que começou a receber propostas de trabalho após aparecer na TV. Uma das empresas que o contratou foi a Ford.
No início da década de 1980, a Ford registrava prejuízos de mais de 3 bilhões de dólares. Deming foi contratado e disse que a gerência era responsável por 85% dos problemas que impediam o desenvolvimento de carros melhores. Os executivos da Ford levaram isso a sério e adotaram as idéias de Deming: em 1986, a empresa se tornou a montadora americana com maior lucro, ultrapassando a General Motors pela primeira vez desde a década de 1920. O lucro cresceu consistentemente nos anos seguintes.
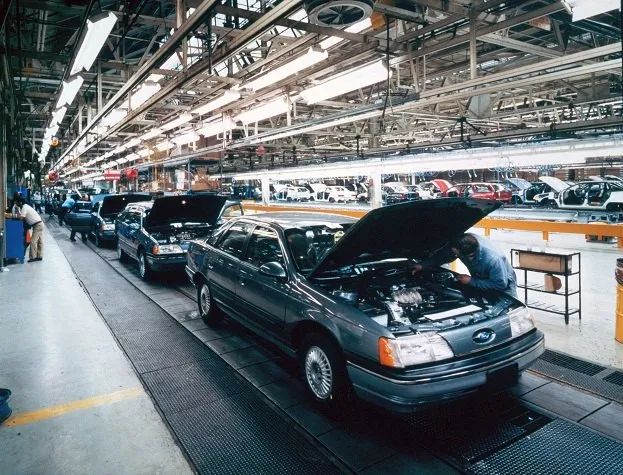
14 pontos para gestão
No livro Saia da Crise, Deming cita os seguintes pontos para a boa gestão de uma empresa:
Criar constância de propósito de aperfeiçoamento do produto e serviço, a fim de torná-los competitivos, perpetuá-los no mercado e gerar empregos.
Adotar a nova filosofia. Vivemos numa nova era econômica. Os executivos e gerentes ocidentais devem despertar para o desafio, conscientizar-se de suas responsabilidades e assumir a liderança em direção à transformação.
Acabar com a dependência de inspeção para a obtenção da qualidade. Eliminar a necessidade de inspeção em massa, focando em fazer certo desde o começo.
Acabar com a prática de escolher fornecedores apenas com base em preço. Em vez disso, minimizar o custo total. Preferir um único fornecedor para cada item, estabelecendo relacionamentos duradouros, calcados na qualidade e na confiança.
Aperfeiçoar constante e continuamente todo o processo de planejamento, produção e serviços, com o objetivo de aumentar a qualidade e a produtividade e, conseqüentemente, reduzir custos.
Fornecer treinamento no local de trabalho.
Instituir liderança. O objetivo da liderança é ajudar as pessoas e máquinas a realizar um trabalho melhor.
Eliminar o medo no local de trabalho.
Quebrar as barreiras entre departamentos. Os colaboradores dos setores de pesquisa, projetos, vendas, compras ou produção devem trabalhar em equipe, para antever problemas na produção ou nos produtos e serviços.
Eliminar slogans, exortações e pedidos para que a produtividade aumente e não ocorram erros. Tais exortações apenas instigam rivalidades entre as pessoas, sendo que o grosso das causas de baixa qualidade e produtividade está no sistema como um todo e não na força de trabalho.
a) Eliminar metas numéricas para o chão de fábrica.
b) Eliminar administração por objetivos — líderes devem conhecer o sistema e prover um plano de trabalho.Remover barreiras que roubem das pessoas o sentimento de orgulho no trabalho. A atenção dos supervisores deve voltar-se para a qualidade e não para números.
Remover barreiras que roubam dos gerentes e engenheiros o justo direito de se orgulhar do produto de seu trabalho. Isso significa abolir avaliações anuais e de mérito, e da administração por objetivos ou números.
Instituir um programa vigoroso de educação e auto-aperfeiçoamento para todo o pessoal.
Empenhar todos na companhia para conseguir essa transformação. É um trabalho de todos.
Fontes e leituras interessantes
- TV Tropes - Japan Takes Over The World - Analysis
- Wikipédia - Lista de países com maiores PIBs históricos
- Duro de Matar, fotografia dos personagens
- BizManualz - How to Use Control Charts for Continuous Improvement
- Wikipédia - William Edwards Deming
- Wikipédia - Walter Andrew Shewhart
- The Deming Institute - The Man
- National Academy of Engineering - W. Edwards Deming
- YouTube - Documentário da NBC "Se o Japão pode, por que não podemos?" (1980) (recomendado)
- Transcrição da palestra de Deming a executivos do Japão em 1950
- Spec Innovations - Ford vs. Mazda transmissions
- Elsmar Quality Forum - The Famous Ford Study of Mazda Transmissions - Can the characteristic be measured?
- New York Times - Management: Ford Embraces Six Sigma (13/06/2001)
A
AlexandreHTRBCampinas/SP,
Brasil